Here at PrimaPorcelain, we're pretty confident that by now you would all have a fairly strong understanding about porcelain and how we believe it is a superior flooring option to its natural stone counterparts. But do you know how porcelain paving is made to make it a better choice? If not, we are here to tell you!
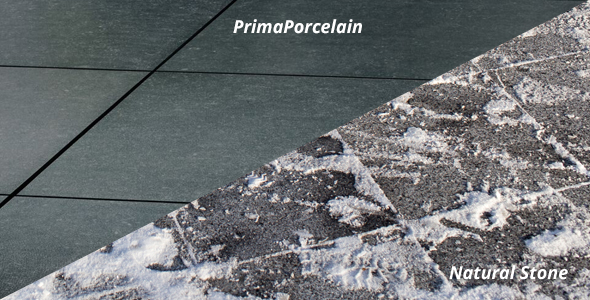
The Manufacturing Process
Porcelain is manufactured using a mixture of sands, clays and other important minerals such as feldspar, which are then baked in a high-temperature kiln. Before the unbaked mixture is sent to the kiln, there is a lot of preparation that is required, followed by a fair bit of post-firing work to ensure the product that is sent out to trade is of a high enough quality and standard. Below we will look at each of these important stages to how porcelain paving is made.
The ingredients
To create the base mixture for porcelain, four ingredients (plus water) are commonly used. These are:
- Feldspar - A granitic mineral from a variety of sources
- High-quality fine clays sourced from Italy, Germany and Turkey
- Kaolin - Also known as China Clay in Britain and Ireland, sourced from Ukraine
- Quartzitic sand - A very pure and fine sand sourced from Germany
Preparation
Very specific quantities of these materials are mixed together with clean, cold water into a slurry, which is then processed in a ball mill to decrease the materials into very fine particles. These particles are so fine the finished product seems like a slippery mud with no discernible grittiness. If you were to rub it between your fingers, it would feel like a fine lubricant, leaving a soft streak across your skin.
Drying
In this muddy form, the mixture of materials is very easy to move around, however, the majority of the water content has to be removed before the mixture can be taken any further. This is performed via a screen drier which utilises hot air and gentle rotation to decrease the moisture levels to approximately 6%. The water that is recovered can then be re-used to create a new initial mixture to keep wastage levels to an absolute minimum.
Storing the Mix
Once the water is removed from the mixture of materials, the dry-ish powder is then kept in a silo until it is required. Different mixes are kept in different silos, with up to 80 silos being held in certain manufacturing plants. Each of these silos holds a slightly different mix, with more or less clay, or a higher proportion of kaolin, for example.
Blending
The next step of the process sees the mixture stored in silos being blended within specialised 'blending towers'. Each tower takes precise quantities of particular mixes from a variety of silos and creates a blend specific to the product that is being manufactured. For example, darker-coloured porcelain might contain more content from silo 19 and less from silo 26, while lighter-colour porcelain might use more from silo 11 and less from silo 7. The secret to producing high-quality porcelain lies in blending the perfect quantities of various mixes to produce the ideal 'biscuit' ready to be baked.
Pressing
The blended powder coming from the towers is then pressed into moulds. Some of these moulds will be smooth with zero surface relief, others will have specific textures or profiled surfaces. Some will be produced in a square-shape, others rectangle. Some will be small, some will be large. The blended powder is subjected to huge amounts of pressure, compacting it into the specific mould, so much so that it turns into a fairly hard material, similar to a biscuit before it is fired in the kiln.
Drying
After pressing, the moisture content of the 'biscuit' is reduced even further from the previous 6% to just 1-1.5% by passing it through another drier, again recovering the water to re-use. The material which emerges from this process is very noticeably harder, tougher, crisper and requires a tough more effort to snap into two pieces.
Finishing Touches
After the material is dried, it is then coloured or printed on and placed in the kiln to be fired. Here this material is carried into the fierce heat of the kiln for around 100 meters, with temperatures reaching as high as 1,200 degrees celsius before going through an equally finely-controlled cooling stage. This cooling stage is just as important as the heating in producing a quality porcelain paver. Once this is over, the tile is then sized to the correct measurements and given additional treatments such as sealants, wax or protective coating before being checked over once more and packed up to be delivered to trade.
This completes the process of how porcelain paving is made. A very delicate process which requires particular attention and detail at each stage. The finished product is a flooring material that offers extremely low-maintenance properties, high resistance to all fading, scratches and stains and overall premium-quality finishes. A material that is long-lasting and gorgeous to look at! You can browse our full collection of porcelain products by clicking below. Order your FREE sample to get a close-up look and see the quality for yourself.
Browse Porcelain Paving >
For more information on our range of porcelain products, be sure to get in touch with a member of the PrimaPorcelain team today!